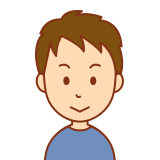
なんだか、在庫管理ができていない、、、。
そんな悩みにお答えします。
☑記事の内容
- 在庫管理の重要性について
- 在庫管理の手法とその特徴
- 実際の現場でおすすめな手法とは?
私は自動車メーカーの工場で改善活動の指導を10年以上行ってきました。実績を金額に換算すると1億円以上の改善を行なってきたいわゆる改善のプロです。
そんな私が解説します。
在庫管理の重要性について
製品や材料の管理をする部門は当然の業務ですが、それ以外の部門においても間接的な切削油や消耗品、事務用品などの在庫管理は必要です。
在庫管理ができていない状態が抱える問題点
在庫管理を適切に行わないと、いつも在庫切れになり困ったり、適正な在庫数量の把握ができていない、、、。なんて事態が起こってしまいます。
在庫が多すぎる場合の問題点
- 運転資金の固定化
- 死蔵品在庫増加
- 在庫関連費用の増加
- 市場対応力・柔軟性の低下
- 保管スペースの増加
運転資金の固定化
在庫は資産であるが、キャッシュではありません。多すぎる在庫は会社の資金繰りに悪影響を及ぼします。
死蔵品在庫増加
多量の在庫を抱えると、新製品の登場などにより陳腐化(古臭くなる、機能が劣る)のリスクがあります。
在庫関連費用の増加
在庫品を購入するための資金の金利、保管コスト、管理費など在庫を抱えるために発生する費用が増加します。
市場対応力・柔軟性の低下
旧モデルが大量に在庫として存在する、古い材料や部品を抱えている場合は新製品への切り替えなどの市場対応力・柔軟性が低下します。
保管スペースの増加
物理的に、在庫が多いと保管するためのスペースが増加します。
h4在庫が少なすぎる場合の問題点
- 品切れによる機会損失増加・信用低下
- 生産期間(納期)の長期化
- 緊急調達増加によるコスト増加
品切れによる機会損失増加・信用低下
在庫が少なければ、品切れ発生リスクが増加します。さらに品切れにより業務への影響が出ると信用の低下につながります。
生産期間(納期)の長期化
調達リードタイム(調達までかかる時間)の長い資材や部品が在庫されていない場合、生産や業務機関の長期化につながります。
緊急調達増加によるコスト増加
在庫切れがが発生し、生産や業務に必要な場合は緊急調達を行います。通常の発注に比べて割高になるケースが一般的でコスト増加につながります。
以上のことから、在庫は多すぎても少なすぎても問題が発生することがわかります。
在庫管理の手法とその特徴
在庫管理は発注するタイミングや量で管理していきます。
- 定量発注方式
- 定期発注方式
- その他の発注方式
定量発注方式
在庫が一定の量(発注点)まで減少した時点であらかじめ設定した一定量を発注する方法です。
発注期間や周期はばらつきますが、発注ごとの発注量は常に同じ(定量)という方式です。
メリット
- 運用・管理が容易
- 事務処理の効率化・自動化が容易
運用・管理が容易
一度発注量を決めてしまえば、その後は面倒な計算も必要なく、在庫量(発注点)だけを管理しておけばよい。
事務処理の効率化・自動化が容易
自動発注への切り替えも可能であり、在庫管理関連の費用を抑えることができる。
デメリット
- 需要変化が激しいものには採用できない
- 調達リードタイムが長いものには不向き
需要変化が激しいものには採用できない
毎回一定量の発注となるため、需要変動が激しいと在庫切れあるいは過剰在庫が発生する。
調達リードタイムが長いものには不向き
調達リードタイムが長くなると、需要変動が発生やすく、またその影響を受けやすいため一定量での発注では対応できない。
発注点の決め方
定量発注方式の発注点は以下の式で計算します。
発注点=調達リードタイム×調達リードタイム中の1日当たり平均需要量+安全在庫
※安全在庫とは、事前に予測することが困難な在庫少量の変動に伴う在庫切れを抑えるために大目に保有する在庫のことです。
安全在庫は品切れ時の影響度や、調達リードタイムの長さ、在庫消費量の変動の大きさなどによって決定します。
発注量の決め方
発注量とは経済的発注量のことです。
1回あたりの発注量を増やせば発注回数が減るため発注処理、受け入れ処理にかかるコスト(葉中関連費用)は減りますが、在庫が増加するため在庫費用が増大します。
逆に1回あたりの発注量を少なくすると、在庫費用は削減されますが、発注関連費用は増加します。
これらの関係を考慮して総費用を最も小さくする発注量を経済的発注量といいます。
- 1回あたりの発注費用 500円
- 在庫品の単価 10,000円
- 年間需要量 10,000個
- 在庫維持費用率 10%
とした場合は以下の計算をします。
経済的発注量=√2×1回あたりの発注費用×年間需要量÷在庫品の単価×在庫費用率
経済的発注量=√2×500×10,000個÷10,000円×0.1=√10,000=100個
となります。
定期発注方式
一定の期間ごとに一定期間の需要量を予測し、それに基づいて発注する方法です。
発注量は毎回異なるが、発注サイクルは常に同じ(定期)という方式です。
メリット
- 精度の高い在庫管理が可能
- 需要変化が激しいものにも対応できる
精度の高い在庫管理が可能
定量発注方式に比べきめ細かな対応が可能であり、在庫量を抑えた管理がかのうです。
需要変化が激しいものにも対応できる
発注ごとに需要予測を行い、需要変動に対応させることができるため、需要変動が激しいものにも対応が可能です。
デメリット
- 管理が複雑で手間がかかる
- 安全在庫が増加する可能性がある
管理が複雑で手間がかかる
発注の都度、需要予測に基づく発注量を計算する必要があり、手間がかかります。
安全在庫が増加する可能性がある
発注サイクルや調達リードタイムが長いと、安全在庫が多くなります。
発注量の決め方
定期発注方式では、発注のたびに発注量を決定します。需要予測などに基づいて計算され、以下の式で計算します。
発注量=在庫調整機関における予想消費量ー(現在の在庫量+発注残)+安全在庫
在庫長関間は発注サイクル+調達リードタイムで求めます。
- 発注サイクル 毎月1回(30日)
- 調達リードタイム 7日
- 予測消費量 1日1個
- 発注残 なし
- 安全在庫 5個
- 4月1日の在庫量 12個
とした場合の4月1日の発注量は以下のようになります。
発注量=在庫調整機関における予想消費量ー(現在の在庫量+発注残)+安全在庫
発注量=(37日×1個)-12個+5個=30個
h3その他の発注方式
その他にも様々な発注方式があります。
- ダブルビン方式
- 補充点方式
- 発注点補充点方式
- 定期補充点方式
- 定期発注点補充点方式
ダブルビン方式
ダブルビン方式は、同容量の在庫の入ったビン(容器、箱など)を2つ用意しておき、一方のビンが空になり、他方を利用し始めたら1つのビンの容量を発注する方式です。
定量発注方式の簡易版です。
補充点方式
補充点方式とは、在庫量が減少したときに、減少した分だけを補充して在庫量を維持しようとする方式です。
補充点方式の発注量=補充点(最大在庫量)-現在の有効在庫量
発注点補充点方式
補充点方式の一つで、在庫量があらかじめ定められた水準に減少したときに最大在庫量(補充点)と現在の有効材料との差を発注する方式です。
定期補充点方式
補充点方式の一つで、あらかじめ定めた補充間隔と最大在庫量(補充点)について定期的に最大在庫量(補充点)まで発注する方式です。
定期発注点補充点方式
補充点方式の一つで、在庫調査間隔、発注点、最大在庫量(補充点)をあらかじめ定めておき、定期的な在庫調査の結果、有効在庫が発注点を下回っている場合に差分を発注する方式です。
実際の現場でおすすめな手法とは?
実際に現場でどの発注方式を採用するのかを判断する方法として「ABC分析」を行います。
ABC分析
ABC分析とは多くの在庫品目を取り扱うとき品目の取扱金額または量の大きい順に並べてA、B、Cの3種に分類し、管理の重点を決めるために行う分析です。
横軸に金額・量の大きい順に品目を、縦軸に累計の金額・量、割合を示したパレート図で分析します。
在庫品目を以下のようにグルーピングします。パレート図の左からA品目、B品目、C品目となります。
A品目
品目別在庫金額上位20%(目安)の品目、これらで在庫金額の80%(目安)に達する
重点管理品目として扱います。欠品を避けるとともに在庫水準を最小になるように管理することが必要です。発注方式は定期発注方式を採用することが一般的です。
B品目
品目別在庫金額上位20%~50%(目安)の品目、これらで在庫金額の15%(目安)を占める
A品目より管理レベルを下げて管理します。一般には定量発注方式を採用しますが、単価の高い品目については定期発注方式を採用します。
C品目
品目別在庫金額上位50%以下(目安)の品目、これらで在庫金額の5%(目安)にしかならない
管理の効率化を最優先します。定量発注方式やダブルビン方式を採用します。
まとめ
記事のまとめです。
- 在庫は多すぎても少なすぎても問題が発生する
- 在庫管理の代表的手法
- 定量発注方式
- 定期発注方式
- その他の発注方式
- 実際の現場ではABC分析を行い、品目ごとに手法を使い分ける
今回は在庫管理について解説しました。
なんとなくで行っている在庫を適切な手法で管理することでコストダウンや欠品リスクの回避につながります。
現場や職場で在庫品を管理していないようでしたら、ぜひ見直してみましょう。