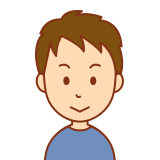
「3ム(さんむ)」を減らしましょうってミーティングで決まったけど、どうすればいいのだろう、、、。
そんな悩みにお答えします。
1,【3ム】のムリ、ムダ、ムラについて理解できるようになります。
2,【3ム】の改善ができるようになるなります。
3,【3ム】を見つけるためのチェックシートを入手できます。
自動車メーカー工場で改善活動の指導・教育を10年以上行ってきたプロが解説します。
改善を進める力をつけたい方は【3ム改善】ムリ、ムダ、ムラを改善するための考え方の記事で考え方を解説していますのでどうぞ。
-1.png)
-1.png)
職場のムリ、ムラ、、ムダについて知ることで改善がはかどるよ!
【3ム、3M】ムリ、ムダ、ムラが潜む職場とは?
現場や職場で使われる「3ム」や「3M」という言葉はムリ、ムダ、ムラの頭文字です。
では、実際の現場や職場でのムリ、ムダ、ムラについて考えてみましょう。
「ムリ」とは
「ムリ」とは目的が手段より大きい状態のことです。
疲れやケガの原因となったり不良や設備の故障につながるような動作や作業です。
例えば、重すぎる、早すぎる、多すぎる、難しすぎる、暑すぎるなどです。
「ムダ」とは
「ムダ」とは目的が手段より小さい状態のことです。
製品を製造するときに付加価値を生まない動作、作業です。
例えば、取り置き、持ち替え、汚れ取り、手直し、調整、調査、過剰などがあります。
「ムラ」とは
「ムラ」とは目的が手段より大きかったり小さかったりする状態のことです。
つまり「ムダ」と「ムリ」が混在している状態のことです。
例えば、作業待ち、作業や出来高のバラつき、能力と負荷のバラつきなどです。
「3ム」が職場にもたらす影響とは?
-1.png)
-1.png)
この「3ム」が現場や職場に存在するとどうなるのでしょうか?
1日の中である時間帯は作業量が多く忙しくなったり、ある時間帯はヒマになり手待ちが増えるといったことが起こります。
これは1日の中でムリな時間帯やムダな時間帯があり1日を通してムラが発生しているということになります。
そうすると、忙しい時間帯は仕事の質より仕事をこなすとこを優先してしまい、品質を犠牲にしてしまう可能性があります。
また、ヒマな時間帯は持て余した時間に合わせて作業をゆっくりと行なってしまい、生産性を犠牲にしてしまうのです。
-1.png)
-1.png)
現場や職場に「3ム」があると品質や生産性、安全性が下がってしまうんだね!
ムリ、ムダ、ムラのチェックシートを公開。気が付くことが改善につながる
ムリ、ムダ、ムラを改善していく手順は単純です。
- 「3ム」に気づく
- ↓
- 「3ム」を減らす方法を考える
- ↓
- 「3ム」を減らす行動をする
-1.png)
-1.png)
最初の手順の「3ム」に気づくことが難しい。チェックリストを活用して発掘すると良いよ!
人に関するチェック項目
- 「ムリ」チェック
- □人間が少なすぎないか
- □もっと楽にできないか
- □人の配置は良いか
- □姿勢、環境、取り扱いなどに無理はないか
- 「ムダ」チェック
- □仕事量と人員のバランスが取れているか
- □手待ち、余裕は多すぎないか
- □適材適所に配置されているか
- □ムダな動きはないか
- □仕事の与えかたにムダはないか
- □計画、段取りが悪いためにムダが発生していないか
- 「ムラ」チェック
- □個人差、人による差はないか
- □バラつきは大きくないか
- □作業量、作業時間は人によって違っていないか
- □人と人の連携動作は良いか
- □一方が作業中のとき、一方が作業待ちになっていないか
- □熟練者の配置は適切か
- □忙しすぎたりヒマになったりしないか
- □作業訓練は平均して行われているか
設備に関するチェック項目
- 「ムリ」チェック
- □機械の能力は十分か
- □保全、点検、修理、交換などは正しく行われているか
- □計測は正しく行われているか
- 「ムダ」チェック
- □機械能力(品質、生産性)は適切に生かされているか
- □機械工具の利用はよいか
- □治工具はよく使われているか
- □自動化、機械化、省力化はよいか
- □標準時間は適切に定められているか
- 「ムラ」チェック
- □生産能力は平均しているか
- □生産能力のバランスはよくとられているか
- □工程負荷は適切か
- □待ち時間、空き時間はないか
資材に関するチェック項目
- 「ムリ」チェック
- □品質、強度、性能にムリはないか
- □納期にムリはないか
- □設計によるムリはないか
- 「ムダ」チェック
- □歩留まりはよいか
- □使えるものを捨てていないか
- □もっと安い材料や資材が使えないか
- □VE(価値分析)はよくできているか
- □作り直し、手直しなど余計な手をかけていないか
- 「ムラ」チェック
- □品質にバラつきはないか
- □性能、形状、寸法、仕上がり、材質などにムラはないか
- □ロットごとに均一か
このチェックリストで現場や職場をチェックしてムリ、ムラ、ムダを発見し改善していきましょう。
【重要】ムリ、ムダ、ムラを改善する前に気をつけるべきこと
ムリ、ムダ、ムラを改善する前に必ず「品質の実績」を把握しておきましょう。
現場や職場の不良率、手直し率、クレーム件数、廃却数、品質のバラつき、等をデータ収集しておきます。
なぜなら、ムリ、ムラ、ムダの背景にクレームや過去の品質トラブルが原因になっていることがよくあるのです。
-1.png)
-1.png)
現場の改善のを進める前に品質データを確認し、その影響を考えながら改善を進めよう。
現場や職場の変えるときには、この作業を変更すると品質にどのような影響を与えるのかを十分意識して行うことが大切です。
せっかくムリ、ムダ、ムラを発見して改善できたと思っても品質クレームが発生したらそれこそ「ムダ」になりかねません。
また、改善後のクレームはその後の改善への悪い影響が出ることも多いので充分注意しましょう。
まとめ
記事のまとめです
- 職場に潜むムリ、ムダ、ムラとは目的と手段のバランスが崩れている状態
- ムリ、ムラ、ムダを発見するにはチェックシートが確実
- 改善は品質の実績を把握してから行う
ムリ、ムラ、ムダの基礎的な解説を行いました。
発見したムリ、ムダ、ムラを改善していくに必要な考え方があります。
こちらの【3ム改善】ムリ、ムダ、ムラを改善するための考え方の記事で解説していますのでどうぞ。