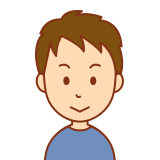
TPMについて詳しくなりたいな、、、。
そんな疑問にお答えします。
☑記事の内容
TPMの心得 第4回
私は自動車メーカーの工場で改善活動の指導を10年以上行ってきました。実績を金額に換算すると1億円以上の改善を行なってきたいわゆる改善のプロです。
そんな私が解説します。
TPMの心得 第4回
- 不具合の発見は五感をフル活用する
- エフ付け、エフ取りで不具合を「見える化」する
- 「マップ」を活用して「見える化」する
- ポカヨケ改善で「うっかりミス」を予防する
- 管理の必要なことは「目で見る管理」を目指す
不具合の発見は五感をフル活用する
不具合とは、正しい状態やあるべき姿にないことです。
不具合の発見には五感を十分に活用することが重要です。
実際に設備を見て、手で触れて、摩耗・破損・発熱を感じたり、異常音や異臭に気づきます。
また、「なんとなくおかしい」という違和感もも五感が総合的に感じ取っている不具合です。
このような不具合を見つけだす活動は全員で行いましょう。
活動を行わない人は不具合に気づく能力が成長せずに、結果としてその人が故障や不具合を発生させてしまうことになります。
見つけた不具合は「正しい元の姿に戻す」し目で見る管理などの工夫をして維持していきます。
エフ付け、エフ取りで不具合を見える化する
「エフ(絵札)」とは、不具合がどこにあるか、どのような不具合かを見える化する道具です。
「エフ付け」とはエフに発見した人の名前や不具合などを記入し、不具合個所に取り付けていく作業です。
「エフ取り」は見つけた不具合を正しい状態に処置した後、不具合がなくなったことを確認し、エフを外す作業です。
「エフ」には自分たちで処理できる問題に付ける「白エフ」と保全部門などの関連部門に依頼し処理する「赤エフ」の2種類があります。
「エフ付け」を行うと設備に絆創膏を貼り付けたように見え、「ここに不具合があるよ、処置してくれ」と訴えかけているように見えます。
エフは「目で見る管理」の道具であり、不具合の見える化の役割をします。
また、他のサークルメンバーが見ることで「これも不具合なんだ」「こんな見方もあるのか」「こんなに細かく見るのか」と気付きを得られることもあります。
エフを付ける不具合例
- 職場や設備の不安全箇所
- 設備の不具合箇所
- 不要物や乱雑な状況などの5Sのできていない箇所
- 作業がやりにくい、きつい箇所
- 守らないと品質不良となる箇所
エフのつける場所は、「目で見える不具合」のほかにも「見えない不具合」も対象です。
例えばVベルトの摩耗が異常に早い場合は「Vベルトの摩耗が異常に速い(2年周期なのに3か月しか持たない)」など記入しその後、原因の追究を行っていきます。
「マップ」を活用して「見える化」する
「マップ」は地図のように何がどこにあるのかを表します。「不具合マップ」や「点検・清掃マップ」や「発生源マップ」など目的に応じて作成します。
全体図や写真などの図表に必要な情報(管理No、部位名称、状況や内容)などを記入して作成します。
複数のマップを組み合わせることで見えてくることもあります。
例えば「チョコ停マップ」と「不安全箇所マップ」を組み合わせると、発生個所が重なるかもしれません。その場合はチョコ停の復旧時に不安全な行動が潜んでいる可能性があります。
その場合だと、不安全行動を取り除くためにはチョコ停への対策が必要なことがわかります。
また、TPMの活動全体を統合した「TPMマップ」を作成し、「改善前やステップ初期」と「改善後やステップ診断後」を比較して活動全体を「見える化」することも効果的です。
ポカヨケ改善で「うっかりミス」を予防する
「ポカヨケ」とは、作業の誤りや部品の付け忘れなどがあった場合ブザーやランプ等で知らせたり、設備そのものが停止することで次に進めないようにする仕組みことです。
ポカヨケ改善を行うためには「ラクに」「早く」「確実に」「安全に」行うためにどうすればよいのかを現場、現物で考えることが必要です。
- 不良や不具合が発生している個所をマップ化する
- ミスをしている状況を4M(人、モノ、方法、設備)で層別する
- 対策案を立案し、実施してみる
- 効果を確認し、納得いくまで改善や調整を行う
作業手順書や作業指示書、工程レイアウト、機械や工具、素材の特性などからポカミスにつながる要因を改善で取り除きます。さらには「ポカミスしない仕組み」や「ポカミスしても次工程へ流出しない仕組み」を構築することが重要です。
管理の必要なことは「目で見る管理」を目指す
「目で見る管理」とは、管理する対象物が自らを異常と判断し、異常自身がその発生を働きかけ、異常への行動処理を的確に人間に行わせる仕組みです。
具体的には、オイルが減ること(管理する対象物)がセンサーを検知させ(減ったことが発生を働きかける)ランプやブザーで表示し給油を促す(以上への行動処理を人間に行わせる)といったことです。
現場では管理する項目が多くあります。そのすべてを集中して監視することには限界があり見逃してしまう可能性があります。
その解決方法として「目で見る管理」があります。設備の異常を設備自らが発信してくれるので管理が行き届きます。また、業務の負荷も減るのでその分を対策防止や改善の時間にすることができるのです。
「目で見る管理」の実践のポイントは以下の3つになります。
- あいまさがない正確・正常な状態に整備する
- 異常が見える・わかる・働きかける仕組みをつくる
- 異常への処置が確実に行える能力を身に着ける
「目で見る管理」を実現して適切な状態を維持管理していきましょう。
まとめ
記事のまとめです
TPMの心得 第4回
- 不具合の発見は五感をフル活用する
- エフ付け、エフ取りで不具合を「見える化」する
- 「マップ」を活用して「見える化」する
- ポカヨケ改善で「うっかりミス」を予防する
- 管理の必要なことは「目で見る管理」を目指す
主に1ステップ~2ステップ活動で役立つ心得を中心にしています。
設備があるべき姿で動くためにも「不良の発見→復元・改善→維持管理」が重要です。
知恵を出し合って「見える化」を行い、適切な維持管理が継続できるようにしていきましょう。
TPM活動の心得はまだまだありますので数回にわけて続けいていきたいと思います。
活発なTPM活動になるよう、心得を全員で共有することも大切です。