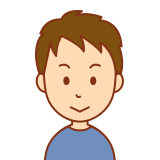
16大ロス、7大ロス、5大ロス、3大ロスっていろんな言い方があるけどどんな違いがあるの?
16大ロス、7大ロス、5大ロス、3大ロスっていろんな言い方があるけどどんな違いがあるの?
そんな疑問にお答えします。
☑記事の内容
- 【16大ロス】人、設備効率、原単位を阻害するロスについて解説
- ロスを改善するとは何をするの?
自動車メーカー工場で改善活動の指導・教育を10年以上行ってきたプロが解説します。
Twitterで改善等の有益な情報を発信しています。フォローお願いします。
【16大ロス】人、設備効率、原単位を阻害するロスについて
16大ロストは「生産の恋率を阻害する16大ロス」のことです。
この16大ロスの中に「人の効率化を阻害する5大ロス」、「設備効率をを阻害する7大ロス」、「設備操業度を阻害するロス」、「原単位の効率化を阻害する3大ロス」があります。
それぞれに解説していきます。
人の効率化を阻害する5大ロス
- 管理ロス
- 動作ロス
- 編成ロス
- 自動化置き換えロス
- 調整測定ロス
人の効率化を阻害するロスとは、「作業者の動作や作業方法、レイアウトなどによる時間的なロス」と「本来の作業以外に行う作業の時間的なロス」です。
管理ロス
管理ロスとは、材料待ち、指示待ち、故障修理待ちなどの管理上発生する手待ちロスのことです。
待っているのに何もしなければこの「管理ロス」です待たない工夫や、他の作業を行うことで改善を進めていきます。
動作ロス
動作ロスとは、動作経済の原則に反する動作ロス、作業者のスキルの差によって発生するロス、レイアウトに起因する歩行ロスなどです。
動作経済の原則とは最小限の労力で最大限の成果を上げるための最良の動作を実現するための基本的な決まり事です。
動作分析を進めてロスを改善を行いますが、歩く、振り向くなどの動作から改善することが簡単で効果が大きいです。
編成ロス
編成ロスとは、多工程持ち・多台持ちにおける手待ちロス、コンベヤ作業のラインバランスロスなどです。
他工程や多台持ちはバランスよく設定します。またコンベア作業においてもバランスが重要です。時間の山や谷を平地にしていくイメージで改善を行います。
自動化置き換えロス
自動化置き換えロスとは、自動化に置き換えることで省人化できるのにそれを行わないために発生している人的なロスです。
作業だけでなく部品の供給や払い出し、運搬などの物流ロスも含みます。
運搬の自動化は費用対効果が大きいのでよく改善の対象になります。小型の自動軌道運搬機(AGV)等の導入により改善していきます。
測定調整ロス
測定調整ロスとは、品質不良の発生や流出防止のため測定、調整を実施するため
のロスです。
安定した品質を確保できなければ改善が困難なロスです。改善の場合には不良品の発生や、流出に十分配慮しましょう。
設備効率を阻害する7大ロス
- 故障ロス
- 段取り・調整ロス
- 刃具交換ロス
- 立上がりロス
- チョコ停・空転ロス
- 速度低下ロス
- 不良・手直しロス
設備効率を阻害するロスは、「設備の負荷時間(設備が動いているべき時間)」と「価値稼働時間(実際に良い製品を作り出した時間)」の差です。
故障ロス
突発的・慢性的に発生している故障によるロスです。時間的なロスと不良による物のロスがあります。
故障とは「機械の停止あるいは機能の低下を伴うもの」「機能の回復に部品交換や修理を伴うもの」「修理に要する時間が5~10分以上のもの」を指します。
「設備の信頼度をいかに高めるか」と「故障してからの回復するまでの時間をいかに短くするか」を考えて改善を進めていきます。
突発的な故障より慢性的な故障に取り組むことが効果的です。
段取り・調整ロス
現製品の生産終了時点から次の製品の切り替え・調整を行い、完全な良品ができるまでの時間的なロスです。
一般的には、生産終了時の治工具の取り外し、片付け、掃除、次の製品に必要な治工具・金具類の準備~取付、調整、試加工、調整、測定、生産(完全な良品)までの流れです。
一発段取りや前段取りといった段取りの時間短縮が主な改善です。特に調整ロスの提言が難易度が高いとされています。
刃具ロス
刃具の定期交換、折損による一時的な高官による時間的なロスと交換の前後に発生する不良品、手直し品といった物のロスです。
刃具の選定はもちろんですが、設備自体の精度、刃物ホルダーの精度でロスが発生していることまあります。
立上がりロス
始業時や、休憩後、長時間停止後の設備立ち上げ時に既定のサイクルタイムで運転しても機械的なトラブルがなく、安定した品質で生産できるまでの時間的ロスと、その間に発生する不良品や手直し品といった物のロスです。
基本的に立上がりロスは設備の熱膨張による変位が原因です。どの部位に、どれくらい、どの方向に発生sているのか?ワークへの影響はどうか?などを調べて改善を進めていきます。
チョコ停・空転ロス
「一時的な機能の停止を伴う停止」「昨日の回復が簡単な処置(異常なワークの撤去とリセット)な停止」「部品交換、修理を伴わない停止」「回復時間が2~3秒から5分未満の停止」とがチョコ停・空転ロスです。
チョコ停は処置が簡単なため見逃しがちですが、大きく効率を阻害している場合があります。
速度低下ロス
設備のスピードが遅いために発生するロスです。
ここでの設備のスピードが遅い状態とは「設計時点のスピード(あるいは品種ごとのスピード)に対して実際のスピードが遅い」「設計時点のスピードが、現状の技術水準またはあるべき姿より遅い」状態です。
設備の設計スピードがわからないケースも多々あります。明確にすることだけで改善につながることもあります。
7大ロスの中でも最も設備効率への寄与度が高いので十分検討する価値があります。
手直し・不良ロス
不良品を修正して良品とするための時間的ロスと手直し・不良による物(廃棄される製品など)のロスです。
突発的な不良より慢性的な不良が放置されがちです。不良ゼロを目指して改善に取り組みます。
設備操業度を阻害するロス
設備効率を阻害するロスに含めて「設備効率を阻害する8大ロス」とする場合もあります。
SD(シャットダウン)ロス
設備の計画的な保全を行うために設備を停止する時間的なロスとその立上がりのために発生する物のロスです。
一般的にはシャットダウン時に行われる清掃、点検、部品交換、オーバーホール、精度チェックなど品質上、安全上、信頼性の維持の面から必要な作業です。
必要な作業ですが、1回あたりの時間短縮、周期の延長、作業の見直しなどを行って改善を進めていきます。
原単位の効率化を阻害する3大ロス
原単位とは物を造るときに必要な原材料やエネルギー、所要時間などのことです。
- 歩留まりロス
- エネルギーロス
- 型・治工具ロス
- 歩留まり(ぶどまり)ロス
「素材重量と製品重量の差」、または「素材投入総重量と製品総重量の差」による物量ロスです。
例えば鋳造工程において製造上廃棄してしまう「バリ」や「湯口」などを減少させていく考えで改善を進めていきます。
エネルギーロス
電力、燃料、蒸気、エア、水(排水処理も含む)などのエネルギーのロスです。
温度や圧力などが本当に必要な量だけ使われているかを見直したり、可変式の制御により省エネ化するなどで改善を進めていきます。
型・治工具ロス
製品を作るために必要な方・治工具の製作、補修にかかる金銭的ロスです。
金型や治工具の摩耗、破損をいかに防止するかを考えて改善を進めていきます。
ロスを改善するとは何をするの?
ロス改善をするとは「現実をしっかり把握して、その問題に対処していくこと」です。
様々なロス分析の手法で現実のロスをしっかり把握します。
その把握したロスを分析し、改善や再発防止策を行っていきます。
そのロスが生産活動の人、設備、原単位のどの部分にどういったロスがあるかをわかりやすくするために「人の効率化を阻害するロス」などで分けられているだけです。
実際のロス改善はほとんどが分析の作業です。
ロス改善を効率的に進めるためにには「どんなロスが隠れているかを分析する力」と「ロスが起きている(発生している)要因を分析する力」を伸ばしていくことが重要です。
まとめ
記事のまとめです
- ロスは16種類ある
- 人の効率化を阻害する5大ロス
- 設備効率をを阻害する7大ロス
- 設備操業度を阻害するロス
- 原単位の効率化を阻害する3大ロス
- ロス改善をするとは「現実をしっかり把握して、その問題に対処していくこと」
- ロス改善を進める重要な能力
- どんなロスが隠れているかを分析する力
- ロスが起きている(発生している)要因を分析する力
16大ロスについてザックリ解説をしていきました。
人、モノ、設備の効率化阻害のロスについて詳しく知りたい方はこちら
ロスは種類が多いため丸暗記はお勧めしません。
なんとなく覚えていて、詳しいことは調べるスタイルをを進めします。
Twitterで自主保全や改善等の有益な情報を発信しています。忘れずにフォローをお願いします。