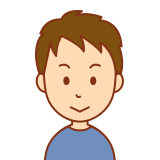
TPMについて詳しくなりたいな、、、。
そんな疑問にお答えします。
☑記事の内容
TPMの心得 第8回
私は自動車メーカーの工場で改善活動の指導を10年以上行ってきました。実績を金額に換算すると1億円以上の改善を行なってきたいわゆる改善のプロです。
そんな私が解説します。
TPMの心得 第8回
- 「段取り改善」に挑戦する
- 「からくり改善」に挑戦する
- 「なぜなぜ分析」を活用する
- 「PM分析」を活用する
「段取り改善」に挑戦する
「段取り改善」とは「段取り・調整ロス」の改善活動です。多品種少量生産、短納期なもの造りを行っている現場には重要な活動です。
設備稼働中の段取り替えは、設備を止めて生産を中断して行うため可能な限り短時間で行うことが求められます。
目標とするのは「一発段取り(シングル段取り)」と呼ばれる超短時間段取りです。現状の10分の1の時間を目標にします。理想は自動車レースのピット作業のイメージです。
段取り改善は3段階で行っていきます。
- 「探す時間」の改善
- 「外段取り」への取り組み
- 「内段取り」の効率化
「探す時間」の改善
段取り替え作業の「探す時間」を改善します。治具や工具、前製品の片づけ、次製品の図面など作業に付随する行動に含まれる全ての「探す時間」が対象です。
整理・整頓を徹底し、探す動作・作業の改善をECRSの法則に基づいて改善を進めます。
「外段取り」への取り組み
「外段取り」とは設備を止めずに行う「あらかじめ準備を行える」段取りです。設備を止めて行う段取りを「外段取り」に移行できないかを検討実施します。
作業内容を層別し、作業内容や手順を見直すことで実施していきます。
「内段取り」の効率化
「内段取り」とは設備を止めて行う段取り作業です。
調整作業の排除や簡易化、脱着作業のワンタッチ化など作業の無駄を改善していきます。
「からくり改善」に挑戦する
「からくり改善」とはからくり人形の代表される知恵と工夫で多彩な動きを実現させる原理を応用した改善です。自動車工場をはじめとする最先端の工場でも取り入れられています。
「位置エネルギー」「慣性の法則」「てこの原理」「重心移動」「視点移動」「リンク機構」などの原理を「歯車」「ゼンマイ」「ワイヤーやチェーン」「バネ」「カムや回転盤」などで活用ます。
「からくり改善」は身近に存在しており、公共施設の入り口に設置してある「足踏み式のアルコール消毒スプレースタンド」も「リンク機構」を利用した「からくり改善」と考えることができます。
TPMにおける点検作業の改善や作業改善など、様々な場面で活用できる改善手法です。
「からくり改善」のポイントとして「お金を少なく知恵を多く」があります。現場のメンバーで知恵を出しあい改善に挑戦してみましょう。
「なぜなぜ分析」を活用する
「なぜなぜ分析」は不具合現象が「なぜ」起きたのかの真因を突き止める、再発棒策を導き出すための手法です。
特徴として、「どんな問題にも、どこでも、誰でも、取り組みやすい」といった手軽さがあります。
「なぜなぜ分析」には2つのアプローチ方法があります。
理想の状態を思い浮かべて原因を探るアプローチ方法の「あるべき姿からのアプローチ」と原理、原則を元に原因を探っていくアプローチ方法を「原理、原則からのアプローチ」があります。
「あるべき姿からのアプローチ」
あるべき理想の姿(状態)と現在の姿(状態)を比較することで問題を探っていく方向を決定し、その後「なぜ」「なぜ」を繰り返しながらその要因を探っていきます。
「原理、原則からのアプローチ」
問題の部分に着目して原理、原則を考えます。その考えた原理、原則を「なぜ」に記入して次の「なぜ」を探っていく方法です。
また、的確な知識や情報があれば誰がやっても最初の「なぜ」はほとんど一緒の結果が出ることも特徴です。
この2つのアプローチで「なぜなぜ分析」に着手することが思いつき改善を防ぐことにつながります。
他記事でなぜなぜ分析のコツを紹介していますので参考にしてください。
「PM分析」を活用する
「PM分析」とはチョコ停や不良、故障などの慢性的な不具合の解決に役立つ手法です。
慢性的な不具合とは、原因と結果が複雑に絡み合った状態で、解決が困難なため見過ごされている状態の不具合のことです。
「PM分析」では原理・原則に従って物理的に不具合を解析し、そのメカニズムを明らかにしていきます。影響する要因を4Mの視点で全てリストアップし、対策を行っていきます。
手順としては4ステップになります。
- 現象を明らかにする
- 物理的解析を行う
- 成立する条件を明確にする
- 4Mで分析し対策を行う
物理的な不具合解析の基本
- エネルギーの受け渡しが行われている加工点はどこかを明確にする
- 絵で加工点を描く
- エネルギーを与えるもの(A)とエネルギーを受けて変形・変質するもの(B)は何かを明確にする
- 変形・変質を形成する物理量パラメータ(C)は何かを原理に基づいて明確にする。物理量とは距離や角度など加工点位置に関係するもの、力・速度・温度・時間などのエネルギーに関係するものがある。
- 物理量パラメータはどのように変化するのか(D)を明確にする
- 「AとBでCがDになる」といった文章表現を行う
- 公式や反応式で表すことができる場合は、それ自体を物理解析と考える
まとめ
記事のまとめです
TPMの心得 第8回
- 「段取り改善」に挑戦する
- 「からくり改善」に挑戦する
- 「なぜなぜ分析」を活用する
- 「PM分析」を活用する
様々な手法や、挑戦的な改善について役立つ心得を中心にしています。
見過ごされがちな「段取り改善」と改善の面白さが詰まった「からくり改善」、分析手法を2つ紹介しました。
TPM活動の心得はまだまだありますので数回にわけて続けいていきたいと思います。
活発なTPM活動になるよう、心得を全員で共有することも大切です。