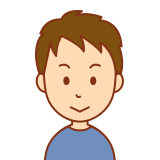
トヨタ生産方式のベースと言われている「IE手法」ってどんな手法なの、、、?
トヨタ生産方式のベースと言われている「IE手法」ってどんな手法なの、、、?
そんな疑問にお答えします。
☑記事の内容
- 【ザックリ解説】IE手法とどんなこと?
- IE手法を使った現場はどう変わる?
- IE手法を現場に取り入れるステップ
私は自動車メーカーの工場で改善活動の指導を10年以上行ってきました。実績を金額に換算すると1億円以上の改善を行なってきたいわゆる改善のプロです。
そんな私が解説していきます。
【ザックリ解説】IE手法とどんなこと?
IEとは「工程管理」の手法です。インダストリアルエンジニアリング(Industrial Engineering)の頭文字をとって「アイイー」と呼ばれます。
生産の工程や作業内容を科学的に管理し、低コストで効率的にもの造りを行い「生産における付加価値」を高めるための技術です。
IEの歴史は古く1700年代後半の産業革命時代から研究されています。現代においても「トヨタ式生産方式」のベースとなり進化を続けています。
IE手法の対象は幅広いものを対象にします。
- 作業者
- 配置
- 習熟
- モラール
- 設備
- 治工具
- 機械
- 材料
- 直接材料
- 関節材料
- 方法
- 工程
- 作業・動線
- 配置
- 時間
- 環境
生産活動を行う人、設備、材料、方法すべてを対象としてIE
手法を活用することで管理、改善を進めていきます。
IE手法の特徴として以下のようなものがあります。
- 分析手順さえ間違わなければ同じ結果が得られる
- 事実を定量的に分析するので検討が行いやすい
- 記号化、図表化することにより共通の言語とし、検討が行いやすい
IE手法は「方法研究」、「作業測定」、「方法研究と作業測定を組み合わせたもの」の3つに分類されます。
方法研究とは、「工程分析」「動作研究」「運搬分析」等の手法で分析します。仕事の流れを分析したり、個々の作業の改善に活用します。
作業測定とは、「時間研究」「稼働分析」等の手法で分析します。作業時間を定量的に測定し、現状分析や評価に活用します。
方法研究と作業測定を組み合わせたものとは、「連合作業分析」、「ラインバランス分析」、「プラントレイアウト」などがあります。
IE手法を使った現場はどう変わる?
IE手法を現場で活用したときに起きる変化です。
手法を使うことによって起きる変化と、実際に現場での変化に分けています。
手法を使うことによって起きる変化
- 勘や経験でなく、系統的、総合的、計画的に状況を把握することができるようになる。また、その事実をもとに分析、検討を行える
- 定量的に系統だった考え方を用いるため、得られた結果から客観的な判断が下せる
- 日ごろ気づかない問題点が浮き彫りにされ、見落としがなくなる
- 不規則な変動の中から規則性を見つけることができる
- 工程全体のチェックを短時間で行うことができる
- 結果が図表や数字で求められるので問題点の把握が容易になる
- 科学的、統計的裏付けがあるので、結果に自信が持て、説得力をつけることができる
- 客観的であるので意見が一つにまとまりやすい
- 状況報告や現状把握の際、説明が簡潔に行える
- グラフなどで状況が一目でわかるので、品質や能率に対する責任と関心を高めることができる
- 作業者自ら手法を用いることにより、作業や工程の理解を深める
実際の現場での変化
- 品質に関わるもの
- 行程不良が減少する
- 作業のケアレスミスが減少する
- 品質特性が向上する
- 市場クレームが減少する
- 製品の品質が安定する
- コストに関するもの
- 原材料の原単位が下がる
- 制度・手続きの合理化から管理経費が削減できる
- 工数の低減、人の有効活用により人件費が削減できる
- 工数・作業標準の明確化から検査試験費用が減少する
- 在庫金利が減少する
- 職場面積の有効活用
- 量に関するもの
- レイアウト、運搬がよくなりモノの流れがよくなる
- 生産量が増加する
- 機械設備、治工具の故障が少なくなり、稼働率が向上する
- 納期遅れ日数、件数が減少する
- 仕掛品が減少する
- 無駄な在庫数量が減少する
- 販売数量が増加する
- リードタイム、ピッチタイムが短縮する
- モラールに関するもの
- 品質意識が向上する
- 意思疎通が緊密となる
- 仕事に関心を持つようになる
- 気軽に話し合える
- 改善に対する必要性、興味がわく
- チームワークが良くなる
- 職場環境がよくなり、整理整頓が行き届く
- 安全に関するもの
- 災害事故件数が減少する
- 疲労が低減する
- 安全衛生に対する意識が向上する
このように大きな変化が現場に現れます。
IE手法を現場に取り入れるステップ
現場にIE手法を当てはめるには「IEによる改善」と「IEによる管理」の
パターンあります。
「IEによる管理」は生産管理的な考え方になるため、今回は「IEによる改善」の進め方について手順を解説します。
「IEによる改善」の進め方
IE改善は他の改善と同じ以下の手順で進めていきます。
- 改善を計画する
- 改善を実行する
- 改善を評価する
改善を計画する
改善を計画するために必要なことを進めていきます。
改善する問題点を見つけ出す
現在や将来において何がどの程度問題なのかを把握するします。そこから得られた問題点を具体的に評価し、適切なテーマを選びます
目標を立てる
取り上げたテーマについてどの程度の成果を期待するのか、その目標を定めます。
計画を立てる
問題解決のための実施事項、手順、協力体制を明らかにし、日程、分担を決め、それに沿った計画書を作成します。
改善を実行する
問題点を詳しく調べる
問題点をより深く掘り下げるために、IE手法などを用いて現状を正しく把握、分析します。
手法の使い方、結果の整理の仕方、結果の見方が特に大切となってきます。
改善案を考える
現状分析の結果に基づいてアイデアを出して具体化し、改善案を立案すします。
改善案を実施する
具体的な改善活動の実施と歯止めまでの過程を計画的に展開していきます。
気を付ける点としては、失敗しても改善を重ねて成功させることです。
改善を評価する
改善の成果を確認する
目標を達成できたかどうかを確認します。
その後、活動全般を振り返り、過程をまとめて今後の課題を明らかにして次回の活動へつなげていきます。
このような手順で進めていきます。
詳細はこちらの記事で詳しく解説をしています。
まとめ
記事のまとめです。
- IE手法とは「生産における付加価値」を高める手法です
- IE手法を現場に取り入れることで、勘や経験でなく、系統的、総合的、計画的に状況を把握することができるようになります。
- IE手法を現場に取り入れるステップは
- 改善を計画する
- 改善を実行する
- 改善を評価する
IEについてザックリ解説をしました。
現場での展開の詳細は別記事で特集しています。
ぜひそちらもご覧ください。