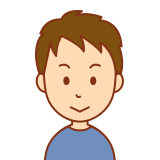
IE手法で現場改善をやってみるか、、、。ってどうやって進めていくんだろう、、、。
そんな悩みにお答えします。
☑記事の内容
- 【IE手法による現場改善】ステップとその進め方~各ステップにおけるおすすめのツールも併せて紹介~
私は自動車メーカーの工場で改善活動の指導を10年以上行ってきました。実績を金額に換算すると1億円以上の改善を行なってきたいわゆる改善のプロです。
そんな私が解説していきます。
【IE手法による現場改善】ステップとその進め方
IE手法による改善の進め方とおすすめのツールを紹介していきます。
- 改善を計画する
- 改善を実行する
- 改善を評価する
改善を計画する
利用手法(IE以外):管理図、特性要因図、ヒストグラム、チェックリスト、5W2H法、ガントチャート
改善する問題点を見つけ出す
「何が問題なのか」「どの程度重要なのか」を明確にします。途中で挫折したり変更することが発生しないように慎重にテーマを検討します。
問題点を見つけ出すには、自身の担当業務や担当工程、作業の実態を十分把握します。その中から部門や上司の方針、目標に関連することを抽出していきます。
問題点の見つけ方
- 部門や上司の方針、目標や運営方針、業務計画などを確認する
- 担当業務を全て書き出して確認する
- 担当工程のデータを収集し解析・分析を行う
担当業務、担当工程で現在困っていること、今後よくしていきたい問題点を抽出し、部門や上司の方針や目標に関連するかを考えていきます。
抽出した問題点や困りごとを層別し、整理する。IE活動として取り組むべき重要な問題点を3つ程度に絞りこみます。
重要問題点について品質、原価、能率などのデータを標準との比較等で問題点を掘り下げ、具体的に評価することで問題点を決定します。
最終的には、上司とのすり合わせにより改善すべきテーマを決定します。
目標を立てる
テーマについてどの程度の成果を期待するのか、具体的な目標を立てます。
業界水準や平均値を目標にすることはNGです。
達成できる確信が持てるギリギリの最高の値を目標とすることが重要です。
目標を立てる方法
目標を立てる方法として以下の5つがあります。
- 方針や事業計画に示されている目標をそのまま利用する方法
- 実績が標準や平均以下の場合、標準値や平均を目標とする方法
- 能率の良い類似工程や類似製品の実績値を目標とする方法
- 過去の改善活動の結果から今回達成できそうだと思われる目標を推測する方法
- 個人的な見解で50%減や20%向上など数値を決める方法
計画を立てる
「改善する問題点を見つけ出す」「目標を立てる」で「どの問題を、いつまでに、どこまで」行うかが明確になりました。「誰が、どのようにして進めていくか」を明らかにしていきます。
問題解決のための実施事項、手順、参加するメンバーなどの協力体制を明らかにし、日程、分担を決めていきます。それをもとに、計画書を作成すします。
改善を実行する
問題点を詳しく調べる
活動計画を作成後、問題を具体化、定量化するために計画に沿って徹底的に現状分析をしていきます。
IEの様々な分析方法を活用して結果を整理し分析します。
- 作業方法の改善の場合
- 稼働率の向上の場合
- ラインバランスの改善の場合
- 運搬・レイアウトの改善の場合
- 標準時間の設定の場合
作業方法の改善の場合
- 工程の実態把握
- 各工程の時間測定
- 動作方法の把握
- 動作経済の原則の適用
工程の実態把握
利用手法:製品工程分析表
やること:工程の順・方法をつかむ、問題工程の作業を把握する
各工程の時間測定
利用手法:PTS法、時間分析法
やること:各工程の時間を正しくつかむ
動作方法の把握
利用手法:動作分析、PTS法
やること:動作の順序・方法をつかむ、作業域の配置を知る
動作経済の原則の適用
利用手法:動作経済の原則
やること:動作経済の原則でチェック、動作上の問題点をつかむ
稼働率の向上の場合
- 非稼働要因の把握
- 稼働状況の実態把握
- 組み合わせ作業の実態把握
非稼働要因の把握
利用手法:特性要因図
やること:非稼働の要因をつかむ
稼働状況の実態把握
利用手法:ワークサンプリング
やること:設備・人の稼働率をつかむ、非稼働要因をつかむ
組み合わせ作業の実態把握
利用手法:作業者ー機械分析
やること:作業者と機械の時間関係をつかむ
ラインバランスの改善の場合
- 工程の実態把握
- 各工程の時間測定
- ラインバランスの測定
- 動作方法の把握
工程の実態把握
利用手法:製品工程分析
やること:工程の順序・方法をつかむ
各工程の時間測定
利用手法:時間分析、PTS法
やること:各工程の時間を正しくつかむ
ラインバランスの測定
利用手法:ラインバランス分析
やること:バランスロス比を求める、ネック工程を把握する
動作方法の把握
利用手法:動作分析
やること:ネック工程、あるいは全行程の動作順序・方法をつかむ
運搬・レイアウトの改善の場合
- 工程の実態把握
- 運搬方法の把握
- レイアウトの実態把握
- 運搬経路の把握
工程の実態把握
利用手法:製品工程分析
やること:工程の順序・方法をつかむ
運搬方法の把握
利用手法:運搬工程分析
やること:運搬の順序、方法、製品の取り扱い方法をつかむ
レイアウトの実態把握
利用手法:配置図、近接性相互関連分析
やること:設備の配置(面積、高さ、方向、置き方など)
運搬経路の把握
利用手法:運搬経路図
やること:製品の運搬経路(流れ)をつかむ
標準時間の設定の場合
- 動作方法の把握
- 作業標準の設定
- 作業の時間測定
- 余裕率の決定
- 標準時間の算出
動作方法の把握
使用手法:動作分析
やること:動作の順序・方法をつかむ
作業標準の設定
使用手法:特になし
やること:標準作業方法を決める
作業の時間測定
使用手法:時間分析、レーディング
やること:作業の正味時間を求める
余裕率の決定
使用手法:ワークサンプリング
やること:稼働率を求める、余裕率を算出する
標準時間の算出
使用手法:特になし
やること:標準時間を算出する
改善案を考える
現状の分析結果にを適切な改善につなげていくために、技術的知識、経験、改善の原則などを組み合わせます。
改善活動において改善案の立案は今までの調査・分析の苦労が形になるところですので特に重要視して行います。
h4改善案を実施する
改善の実施内容を含め計画的に実施していきます。
改善の実施で考慮すべきことは以下の5つです。
- 最初の問題に立ち返る
- 改善を実施することにより、問題が十分に解決されるかを考える
- 経済性の検討を加える
- 改善案がもたらす効果の正確な評価と改善に必要な経費との比較検討を行う
- 必ず試行の期間を設ける
新しいものや方法は不安定なことが多いです。試行期間を設け、その後本実施に移行します。
実施のための説明を行う
改善は現状からの変化があるため抵抗があることも多いです。説明する機会を設けたり、立案に参加してもらうなど、抵抗を下げる工夫を行います。
改善事項を歯止めする
改善事項を維持するために歯止めを行います。
- 標準作業を改定する・理由も必ず併記する
- 繰り返し指導や訓練を行い新しい作業標準を守る(守らせる)
- 改善事項の管理方法を決めフォローする
- 物理的に改善前に戻らない工夫をする
改善を評価する
改善の成果を確認します。客観的視点で目標を達成できたかどうかを確認することが重要です。
評価後は、活動全般を振り返り、過程をまとめて今後の課題を明らかにすることで次回の改善につなげていきます。
以上がIE手法の進め方です。
まとめ
記事のまとめです。
IE手法による改善活動は
- 改善を計画する
- 改善を実行する
- 改善を評価する
の3ステップで実施していきます。
当たり前の手順ですが重要です。
漏れがないように進めていきましょう。