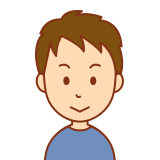
設備の管理って重要だよな、、、。どうやるのだろう、、、?
そんな疑問にお答えします。
☑記事の内容
- 【種類が多くあります!】設備保全とは?
- 設備の評価方法について知ろう。
- 設備保全を行う際に注意すべき落とし穴 3つ
私は自動車メーカーの工場で改善活動の指導を10年以上行ってきました。実績を金額に換算すると1億円以上の改善を行なってきたいわゆる改善のプロです。
そんな私が解説します。
【種類が多くあります!】設備保全とは?
設備保全とは、「設備性能を維持するために、設備の劣化防止、劣化測定および劣化回復の諸機能を担う日常的または定期的な計画、点検、検査、調整、整備、修理、取換などの諸活動の総称」とJISで定義されています。
つまり、設備の技術的な性能を維持するため行う活動の総称が設備保全です。
保全とは、設備のライフサイクル全般から故障の排除を行うために計画、点検、検査、調整、修理、取替などを行う活動です。
保全を行うことを保全活動と呼び、設備を正常、良好な状態に保ち、効率的な生産活を維持していきます。
保全活動は以下の2つに分類できます。
- 維持活動
- 改善活動
維持活動
設備の維持活動は設計時の技術的な性能を維持する活動です。
予防保全と事後保全に分けることができ、予防保全はさらに2つに分けることができます。
予防保全
予防保全は「故障に至る前に寿命を推定して、故障を未然に防止する方式の保全」です。
生産停止や速度低下などの性能低下をもたらす状態を発見するために点検や診断を行うことや、故障の前兆を察知して調整や修復を行います。
設備の管理は基本的にこの予防保全で行われるべきであるとされています。
点検や診断を行うことを予知保全といいます。
予知保全とは「設備の劣化傾向を設備診断技術などによって管理し、故障に至る前の最適な時期に最善の対策を行う予防保全の方法」と定義されています。
故障の前兆を察知して調整や修復を行うことを定期保全と呼ばれます。
定期保全とは「従来の故障記録、保全記録の評価から周期を決め、周期ごとに行う保全方式」と定義されます。
一般的にイメージされる保全活動になります。定義の中にもあるように故障記録や保全記録から定期保全の周期を決定することで運用していくため以下のポイントがあります。
周期の見直しを常に行い最適な保全周期を見極める
故障や定期保全で交換、調整した項目について定量的に評価する
稼働時間だけでなく、ショット数、経過時間、使用用途な出様々な側面から周期を測定する
事後保全
事後保全とは「設備に故障が発見された段階で、その故障を取り除く方式の保全」と定義されています。
事後保全の際にはその故障を分類する必要があります。
- 故障部位そのものの部品や設備の寿命で故障した
- 突発的な扱い不良等で故障が発生した
- 他の要因(ほかの部品の摩耗)で故障部位が故障した
- 原因不明
この4つに分類することで再発防止を行い、故障による生産効率の低下を予防します。
改善活動
改善活動は性能劣化を修復・改善する活動です。
改良保全と保全予防の2つの活動があります。
改良保全
改良保全とは、「故障が起こりにくい設備への改善、または性能向上を目的とした保全活動」と定義されています。
設備の構成要素や部品の材質、使用する部品の改善、構造の設計変更などを行います。
活動の効果として、稼働条件を改善したことによるサイクルタイムの短縮や生産効率の向上、工具や刃物の寿命延長などがあります。
保全予防
保全予防とは、「設備、系、ユニット、アッセンブリ、部品などについて、計画・設計段階から過去の保全実績または情報を用いて不良や故障に関する事項を予知・予測し、これらを排除するための対策を織り込む活動」と定義されています。
要約すると故障しにくい設備を設計する活動ということです。
設備の評価方法について知ろう。
- 設備総合効率
- そのほかの評価指標
設備総合効率について
ほとんどの場合、設備の評価は「設備総合効率」で行います。
負荷時間を100%として、どのくらいの時間、どのくらいの性能で、どのくらい良品を生み出したかを表します。
設備総合効率=時間稼働率×性能稼働率×良品率
で計算されます。
設備の効率を阻害する要因として「停止ロス」(故障停止、段取り・調整、刃具交換、立ち上がり「性能ロス」(空転。チョコ停、速度低下)「不良ロス」(不良、手直し)などがあります。
停止ロスの大きさを時間稼働率で示します。
計算式は以下になります。
時間稼働率=(負荷時間ー停止時間)÷負荷時間×100(%)
性能ロスの大きさを性能稼働率で示します。
計算式は以下になります。
性能稼働率=(基準サイクルタイム×加工数量)÷稼働時間×100%
不良ロスの大きさを良品率で示します。
計算式は以下になります。
良品率=(加工数量ー不良数量)÷加工数量×100%
これらの3つの割合を掛け合わせて設備総合効率とし、設備の使用効率の度合いを示し設備効率を総合的に評価します。
その他の評価指標
設備の故障のしにくさや修復のしやすさを、稼働時間や修復時間など時間の観点から評価する指標があります。
- 故障平均間隔(MTBF)
- 平均修復時間(MTTR)
- 可用率(アビラビリティ)
故障平均間隔(MTBF)
故障平均間隔とは、「故障設備が修理されてから、次に故障するまでの動作時間の平均値」と定義されています。
設備の信頼背を評価する指標で、大きいほど信頼性が高いです。計算式は以下になります。
故障平均間隔=使用時間の和÷故障回数
平均修復時間(MTTR)
平均修復時間とは、「故障した設備を運用可能状態へ修理するために必要な時間の平均値」と定義されています。
設備の保守性を評価する指標で、小さいほど保守性が高いです。計算式は以下になります。
平均修復時間=修復時間の和÷修理回数
可用率(アベイラビリティ)
可用率とは、「必要とされるときに設備が使用中または運転可能である確率」と定義されています。
設備の可用性を評価する指標で、大きいほど良いとされています。計算式は以下になります。
可用率=平均修復時間÷(平均使用時間+平均修復時間)
設備保全を行う際に注意すべき落とし穴 3つ
設備保全は積極的に行うべきものですが、注意点が3つあります。
- 定期保全での交換部品がいつまでも同じ
- 予防保全を行いすぎて年間コスト○○万円
- 設備の部品は常に最新式
解説していきます。
定期保全での交換部品がいつまでも同じ
定期保全(1週・1月・3月・半年・一年)での交換部品に変化がない場合があります。
問題なく保全されているようですが、問題が隠れています。
定期保全の交換部品がいつまでも同じということは、常に見直しを行う観点が抜けているからです。
定期交換品を上級グレードのものに変更して期間の延長を行ったり、定期的に消耗する部品については構造的な対策を検討するなどの活動が必要です。
予防保全を行いすぎて年間コスト○○万円
予防保全を行い故障ゼロの状態を維持することは設備保全の理想の状態です。
しかし、年間のコストはいくらでしょうか?
故障ゼロと年間の保全コストを常に意識して保全活動を行う必要があります。
設備の部品は常に最新式
設備の改善を重ね、設備のセンサーは常に最新式といった場合があります。
基本的に設備のセンサーとは必要最低限でよい場合がほとんどで、最新のセンサーを必要とする場面は少ないはずです。
採用しているセンサーがメーカーさんのおすすめで検討不十分で取り付けている場合は見直しが必要な場合があります。
まとめ
記事のまとめです。
- 保全活動は2つに分類できます。
- 維持活動
- 改善活動
- 設備の評価は「設備総合効率」で計行う。
- 設備総合効率=時間稼働率×性能稼働率×良品率
- 設備保全を行う際に注意すべき落とし穴
- 現状に満足せず、費用対効果を考慮した設備保全が重要
保全活動についての知識面を解説しました。
実際に保全を行う立場ではなくても、コスト管理や業務改善には必要な考え方です。
常に、何のための保全かを意識して、費用対効果を追い求めましょう。