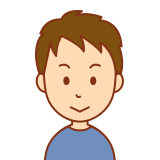
ロスをがどのくらいあるのか計算できるのかな、、、。
設備総合効率って何だろう?
そんな疑問にお答えします。
☑記事の内容
- 【ロス改善は数字で表現】ロス改善の計算とは?
- ロス改善に関連する計算【人の効率化】
- ロス改善に関連する計算【設備の効率化】
- ロス改善に関連する計算【原単位の効率化】
私は自動車メーカーの工場で改善活動の指導を10年以上行ってきました。実績を金額に換算すると1億円以上の改善を行なってきたいわゆる改善のプロです。
そんな私が解説します。
【ロス改善は数字で表現】ロス改善の計算とは?
ロスは計算で求められます。ですから、ロス改善の効果も計算できるのです。
ロスを計算で求めることによって「ロスが定量的にわかる」といったメリットがあります。
改善前と改善後の状態を計算し、比較することで「ロス改善の効果」を定量的に表現することができます。
定量的とは物事の様子を数字で表すことです。
特に報告や集計時には第三者にもわかりやすくするため、定量的に表現する必要があります。
「段取りロスを4か所改善しました。」より「段取りロスの改善により時間稼働率を80%から87%に向上させました。目標は95%です。」のほうがわかりやすいのです。
人の効率、設備の効率、原単位の効率それぞれに計算方法があります。
計算方法とがどのロスと関連しているのかを次項から解説します。
数が多いのでその都度調べることで十分です。
自主保全士の資格を獲ろうと思う方は覚える必要があります。
ロス改善に関連する計算【人の効率化】
人の効率化の計算です。
- 時間稼働率
- 能率
- 総合効率
- 省人化率
について計算します。
この計算に必要な数字(数値やデータ)は
就業工数
会社が賃金を支払う対象となる時間、通常は1日8時間で計算する。
負荷工数
就業工数から除外工数(他部門応援)、休憩時間、朝礼時間などを引いた工数。
実際に生産計画を達成するために人が作業しなければならない時間です。
この負荷工数を100%価値に近づけるることがロス改善の目標です。
正味作業工数
負荷工数から「管理ロス」、「動作ロス」を引いた工数。
負荷工数から指示待ちや材料待ちの時間といった「管理ロス」と、故障、段取り、立ち上がりなどの設備停止の時間、部品や道具を準備る時間などの「動作ロス」を引いた実際に作業に投入した時間です。
有効工数
正味作業工数から「編成ロス」、「自動化置き換えロス」を引いた工数。
正味作業工数から人員配置のアンバランスさによる時間、非定常作業の発生に伴う時間といった「編成ロス」と、自動化が不十分なため発生している時間の「自動化置き換えロス」を引いた実際に作業している時間です。
価値工数(出来高工数)
有効工数から「調整測定ロス」を引いた工数。
有効工数から不良・手直しにかかった時間、品質が不安定なため頻繁に測定を行う時間といった「調整測定ロス」をひいた実際に出来高に結びついた時間です・
各数字とロスの関係を見てみると
管理ロス、動作ロス
負荷工数から正味作業工数を引いたものすべて
編成ロス、自動化置き換えロス
正味作業工数から有効工数を引いたものすべて
調整測定ロス
有効工数から価値工数を引いたものすべて
以上が計算に必要な数字(数値やデータ)となります。
時間稼働率
時間稼働率は負荷工数の中にどのくらい正味作業工数があるのかを率で表します。
時間稼働率=正味作業工数÷負荷工数×100
実際に負荷工数が400分、正味作業工数が320分だった場合は
360÷400×100=90 時間稼働率は90%となります。
つまり100%-90%=10% 負荷工数の10%は管理ロスや動作ロスといった作業ロスだということがわかります。
能率
能率は正味作業工数の中にどのくらい価値工数(出来高工数)があるのかを率で表します。
能率=価値工数÷正味作業工数×100
実際に賞味作業工数が320分、価値工数が224分だった場合は
244÷320×100=70 能率は70%となります。
つまり100%-70%=30% 正味作業時間の30%は編成ロスや自動化置き換えロス、測定調整ロスだということがわかります。
総合能率
総合能率は負荷工数の中にどのくらい価値工数(出来高工数)があるのかを率で表します。
総合効率=時間稼働率(整数)×能率(整数)×100
実際に時間稼働率が90%(整数で0.9)、能率が70%(整数で0.7)だった場合は
0.9×0.7×100=63 総合効率は63%となります。
100%-63%=37% 負荷工数の637%はロスであるということがわかります。
省人化率
どのくらい省人化ができたかを表す数字です。
人数で表すともとの人数により1人の価値が変動するので率で表します。
省人化率=改善後の配置人員÷現状の改善人数×100
実際に現状が10人、改善後は7人だった場合は
7÷10×100=70 省人化率は70%ということになります。
つまり改善によって70%の人員で業務が行えるということです。
ロス改善に関連する計算【設備の効率化】
設備の効率化の計算です。
- 時間稼働率
- 性能稼働率
- 良品率
- 設備総合効率
について計算します。
この計算に必要な数字(数値やデータ)は
操業時間
1日または月間を通じて設備が稼働しうる時間です。
負荷時間
1日または月間を通じて設備が稼働しなくてはならない時間です。
操業時間から生産計画上の休止時間、保全のために休止時間、朝礼時間などを引いた時間です。
実際に生産計画を達成するために設備が稼働しなければならない時間です。
この負荷時間を100%価値に近づけるることがロス改善の目標です。
稼働時間
負荷時間から「故障ロス」「段取りロス」「刃具交換ロス」そのほか停止時間を引いた時間です。
実際に設備が稼働した時間になります。
正味稼働時間
稼働時間から「立ち上がりロス」「チョコ停・空転ロス」「速度低下ロス」を引いた時間です。
価値稼働時間
正味稼働時間から「不良・手直しロス」を引いた時間です。
実際に製品(良品)を生産した時間です。
各数字とロスの関係を見てみると以下のようになります。
故障ロス、段取り、調整ロス
負荷時間から稼働時間を引いたものすべて
立ち上がりロス、チョコ停・空転ロス、速度低下ロス
稼働時間から正味稼働時間を引いたものすべて
不良・手直しロス
正味稼働時間から価値稼働時間を引いたものすべて
以上が計算に必要な数字(数値やデータ)となります。
時間稼働率
時間稼働率は負荷時間の中にどのくらい正味稼働時間があるのかを率で表します。
時間稼働率=稼働時間÷負荷時間×100
実際に負荷時間が400分、稼働時間が320分だった場合は
360÷400×100=90 時間稼働率は90%となります。
つまり100%-90%=10% 負荷時間の10%は故障ロスや段取り・調整ロスといった停止ロスだということがわかります。
性能稼働率
性能稼働率は正味稼働時間の中にどのくらいの性能を発揮したのかを率で表します。
性能稼働率=(サイクルタイム×個数)÷稼働時間×100
実際に稼働時間320分、サイクルタイム2分、個数122個の場合は
(2×122)÷320×100=70 性能稼働率は70%となります。
つまり100%-70%=30% 稼働時間の30%は立ち上がりロス、チョコ停・空転ロス、速度低下ロスだということがわかります。
良品率
どのくらい良品を生産したかを表す数字です。
個数で表すと1日の生産個数に1個の価値が変動するので率で表します。
良品率=(加工数量ー不良数量)÷加工数量×100
実際に加工数量がが122個、不良品が12個だった場合は
(122-12)÷12×100≒90.16 良品率は約90%ということになります。
つまり製品の90%ぐらいが良品ということです。
設備総合能率
総合能率は負荷時間の中にどのくらい付加価値をうみだしているのかを率で表します。
設備総合効率=時間稼働率(整数)×性能稼働率(整数)×良品率(整数)×100
実際に時間稼働率が90%(整数で0.9)、性能効率が70%(整数で0.7)、良品率が90%(整数で0.9)だった場合は
0.9×0.7×0.9×100=56.7 設備総合効率は56.7%となります。
100%-56.7%=43.3% 負荷工数の43.3.%はロスであるということがわかります。
ロス改善に関連する計算【原単位の効率化】
原単位のロスの計算です。歩留まりロスに関しては向上率、エネルギーロス、型・治工具ロスについては削減率で表します。
- 歩留まり向上率
- エネルギー削減率
- 型・治工具ロスの削減率
について計算します。
歩留まり向上率
歩留まりロス改善によってどのくらい改善したかを率で計算します。
歩留まり向上率=【1-(改善後の材料投入の総重量÷現状の投入材料の総重量)】×100
エネルギー削減率
エネルギーロス改善によってどのくらい改善したかを率で計算します。
エネルギー削減率=【1-(改善後の投入エネルギー÷現状の投入エネルギー)】×100
型・治工具ロスの削減率
型・治工具ロスの改善によってどのくらい改善したかを率で計算します。
型・治工具ロスの削減率=【1-(改善後の投入金額÷現状の投入金額)】×100
まとめ
記事のまとめです。
- ロス改善の効果は計算できる。
- 計算で求めることによって「ロスが定量的にわかる」といったメリットがある。
- 人の効率、設備の効率、原単位の効率それぞれに計算方法がある。
ロス改善の計算について解説しました。
効果の確認には必ず数字で定量的に表現するようにしましょう。